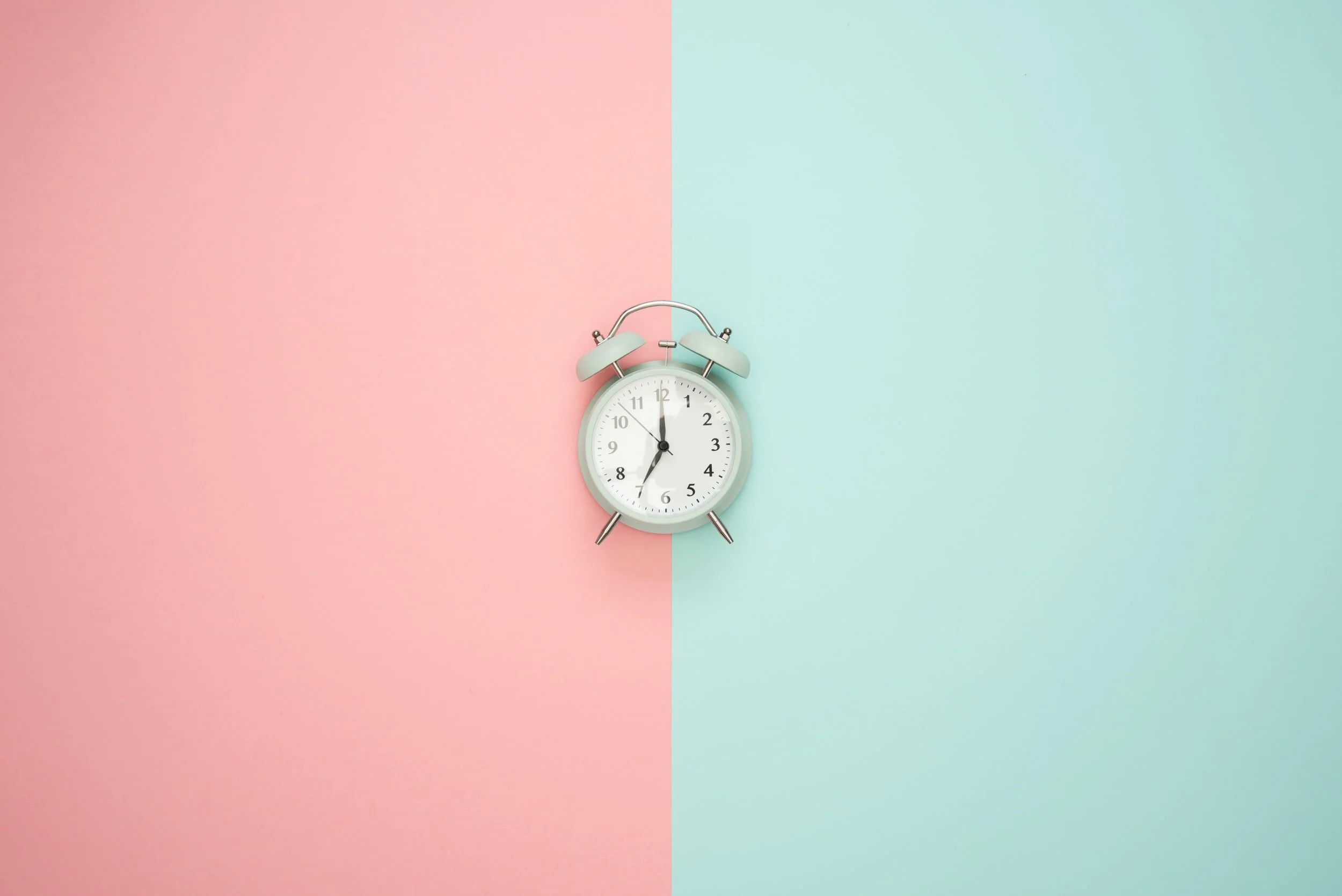
LOST TIME ANALYSIS (LTA)
Every process has losses that reduce output. Lost time is waste and we strive to eliminate it to improve our efficiency.
Lost time can be categorised into:
Availability – Losses that affect how much time is available for work
Performance – Losses that affect how quickly (the rate) that we do work
Quality – Losses associated with defects / poor quality items
By measuring our and analysing lost time, we can start to understand where our losses are coming from. By applying practical problem solving methodology, we can then start to eliminate root cause.
To be effective, Lost Time should be measured as part of our daily routine and visible where the work is being carried out.